A set of equations can be derived for the surface location within the sponge and depends upon the sponge geometry. For example, the surface within a sponge with radial sponge panels (as illustrated above) is defined by:
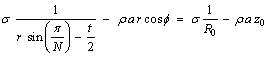
Solving this equation for a specific sponge and across a variety of reference conditions reveals a couple of interesting phenomenon.
First, at a sufficiently high lateral acceleration, the propellant need not be continuous and can reside within two separate regions of the sponge. This could create isolated, inaccessible propellant within the sponge and occurs if
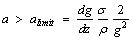
|
|
Second, the surface depends upon a reference surface location and radius of curvature (0 subscript). The initial position will be defined by the leak paths (or drip path) near the sponge. The final position will be dictated by the porous element pick up near or within the sponge.
The leak path is particularly important. If a PMD structure, such as a vane, is too close to the sponge, all of the sponge propellant may leak out via the vane - rendering the sponge useless. An example of this in one g can be demonstrated by considering a household sponge suspended in mid air vs. one sitting on a paper towel which extends over a counter. In the later case, the paper towel is a leak path and much of the water in the sponge will leak out leaving less liquid behind for use. Properly controlling the leak path is essential for maximum sponge performance.
For more information on the design, use, and physics of sponges please see
AIAA 93-1970 Propellant Management Device Conceptual Design and Analysis: Sponges |